Slotting Machine Tool Holder
Over the years, we’ve written a lot of articles about toolholders for milling machines. They’re an important topic and I frequently get questions about them. /dania-beach-slot-machines.html. Recently, I found myself having to visit multiple CNCCookbook articles to answer a question and decided it was time to get all the information into one article along with refreshing the research and seeing what new information I could add. In addition, I wanted to make as much of the information tabular as possible to make it easy to refer to. Here’s what I came up with:
- Slotting Machine Tool Holder Organizer
- Slotting Machine Tool Holder Suction Cup
- Slotting Attachment For Milling Machines
- Turbo Turn specials deliver your tools optimized for your unique application to maximize machining productivity. Parlec has invested in the latest CNC machine technology and software at our Fairport, NY facility, increasing our manufacturing capacity. Dedicated CNC cells allow us to develop custom tool holders to your exact specifications,.
- The slotting head has a 0.625' socket for the tool holder to sit in. Can anyone provide a sketch of something that will work? I am anticipating using 1/4' square HSS tool bits for the 1/4' keyway and had thought of clamping it horizontally in the bottom of the tool holder.
- SLOTTING TOOL HOLDER. Machine manufacturer: Machine model: Category: Mouse move on Image to zoom. SLOTTING TOOL HOLDER. Part number: NKM0930100 Catalog page.
- Solid round tools. The solid round tools' range covers all application types within the areas of solid carbide drilling, milling, HSS tapping, reaming, and threading. Each solid round tool is designed to fulfill the demands of high quality, precision, and maximum productivity, enabling you to get the most out of your machining process.
- IMTS Spark: Techniks has expanded its line of hydraulic tool holders with the Triton line of hydraulic chucks. Horn USA's W&F Linear Unit Quick-Change System Improves Tool Change Repeatability. IMTS Spark: The W&F linear unit with coolant management from Horn USA is a user-friendly quick-change system that can be combined with W&F Micro.
For each toolholder type, there are multiple rows with scores from 1 to 4, where a higher score is better. 4 is the best score and 1 is the worst.
Lunas code collection online double u casino. Luna's Code Collection. 3,908 likes 29 talking about this.
It is a cutting tool that is especially designed for slotting machine. Features of the HSS include a pin, which allows the mounting system of the cutting tool to be quick and self-centering. Depending on the client's request, the robust tool holder can also be supplied with boring for the flow of cooling fluid.
Let’s go over each row and what it means.
Precision
To achieve precision, you’ll need low runout and repeatability for the tool holder. The Weldon-style set screw holder has the lowest precision because set screws against a flat on the tool shank will push the tool off center and because you can’t guarantee repeatability since a slight rotation of the shank will change the exact point at which the setscrews engage.
Slotting Machine Tool Holder Organizer
Versatility
This is simply a measure of how many shank sizes a single toolholder of the type can accommodate. In theory, greater versatility means you’ll need fewer toolholders.
Ease of Use
This is a measure of how easy it is to setup a cutter in the toolholder or take it back out. Nothing could be easier than using a set screw holder–just stick a cutter in and tighten the set screws. The Shrink-Fit holder requires the use of a heat shrink machine to do anything. In the middle are toolholders that require proper assembly torque.
This is a good time to put in a plug for proper ER collet chuck torquing. For best performance, they require a lot more torque than most machinists realize. That torque goes to keeping the tool clamped so it won’t pull out and to making the whole assembly rigid so it resists vibration and chatter.
When you hear a machinist talking about having an endmill slip in an ER collet chuck, you have to wonder two things:
– How clean was the chuck and cutter shank when they were tightened together? The slightest residue of oil or cutting fluid can rapidly reduce the collet’s holding power.
– How much torque was used to tighten the collet nut?
Consider the following torque specs from Technik USA:
Collet | Nut Type | Collets I.D. | Collets I.D. |
OVER 1/16″ (2mm) | UNDER 1/16″ (2mm) | ||
ER 16 | slotted | 42 ft/lbs | 30 ft/lbs |
ER 16 | hex | 42 ft/lbs | 30 ft/lbs |
ER 20 | slotted | 59 ft/lbs | 24 ft/lbs |
ER 20 | hex | 59 ft/lbs | 24 ft/lbs |
ER 25 | slotted | 77 ft/lbs | 77 ft/lbs |
ER 25 | mini nut | 25 ft/lbs | 25 ft/lbs |
ER 32 | slotted | 100 ft/lbs | 100 ft/lbs |
ER 40 | slotted | 130 ft/lbs | 130 ft/lbs |
Are you torquing your ER32 collets to 100 ft/lbs? That’s a bunch more than a lot of folks expect going on feel alone.
Whether you use a torque wrench or not, and Technik as well as others make appropriate adapters, make sure you’ve at least got a nice wrench for your chuck. The single pin spanners are the worst for me when I have to apply a lot of torque. In addition, you’re going to need a way to solidly mount your collet chuck while you tighten the nut. Bench fixtures are the most helpful for this task.
Reliability
This is a measure of how much maintenance is needed to keep the toolholder performing to spec. Set screw holders are dead easy as are shrink-fit–no moving parts. Collet chucks and milling chucks need to be kept clean and torqued to proper specs.
High Speed
This row scores the suitability of different toolholders for higher spindle speeds. “High” starts in the 8000-10,000 rpm range and the primary requirement is the ability to balance the toolholder well. Less mass in the toolholder will also help because the less mass that’s spinning, the less vibration at a given level of balance.
Slotting Machine Tool Holder Suction Cup
Working well with high speed spindles is one of the biggest reasons to invest in fancier toolholders.
Surface Finish and Roughing
These two categories get into suitability for task. For surface finish, we need to keep the modal stiffness high to resist vibration. For roughing finish, we want high dynamic stiffness to resist chatter under varying loads, rpms, and frequencies, and we want strong clamping on the tool to resist the higher forces of roughing.
Cost
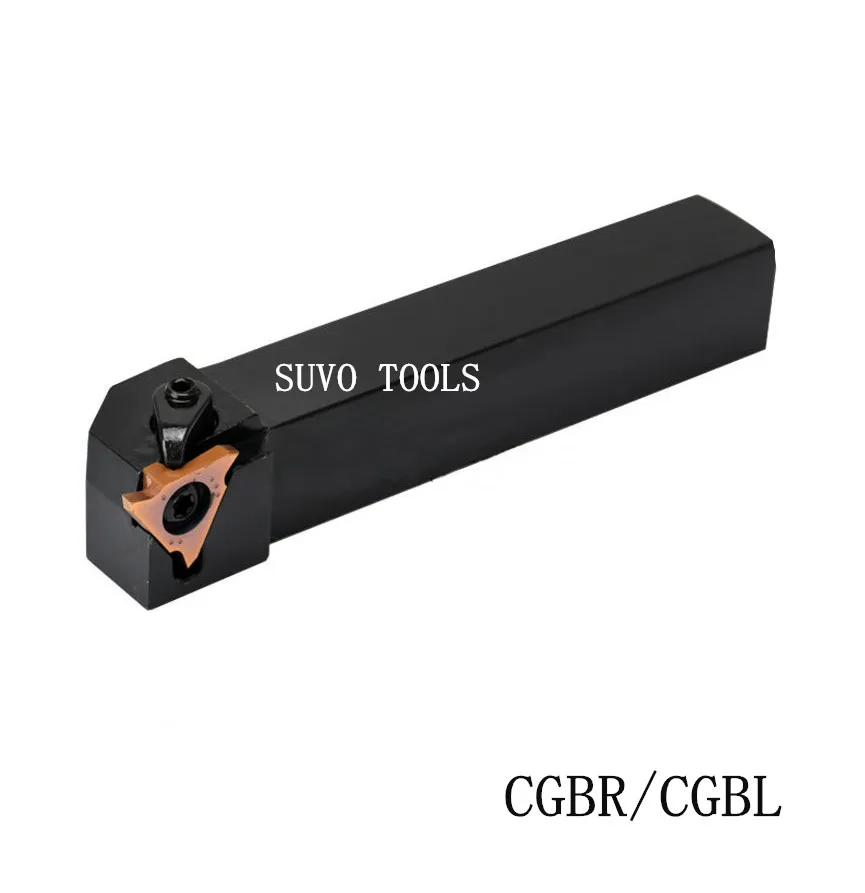
Cost is near and dear to everyone’s pocketbook, and the costs vary quite a lot between these various toolholders
Best Application
Drumroll please, this is the one we’ve been waiting for: what’s the best situation for each toolholder type?
This bears recapping:
– For your absolute highest MRR milling and drilling applications, consider a Side Lock or Weldon Shank-style toolholder. We’re talking big indexable tooling for the most part, not solid endmills.
– For mid-sized milling and drilling, consider a Milling Chuck. This is your largest solid endmills and twist drills, say 3/4 to 1″ and up. Also consider these when you have chatter problems on your big tooling using a Side Lock holder.
– For lighter milling and drilling, consider an ER collet chuck. Anything 3/4″ or under makes sense.
Slotting Attachment For Milling Machines
– For high rpm applications, consider shrink fit toolholders.
Obviously there is some gray area of overlap in each of these cases, but this should serve as a good starting point for toolholder selection.
Like what you read on CNCCookbook?
Join 100,000+ CNC'ers! Get our latest blog posts delivered straight to your email inbox once a week for free. Plus, we’ll give you access to some great CNC reference materials including:
- Our Big List of over 200 CNC Tips and Techniques
- Our Free GCode Programming Basics Course
- And more!
Just enter your name and email address below:
100% Privacy: We will never Spam you!More articles you may like:
The motorized slotting head is the new slotting system for CNC lathes with motorized tool holders. The experience gained during these years in slotting machining gave BRIGHETTI MECCANICA the capacity to understand the biggest set of problems operators meet during a slotting machining and to develop correct solutions to apply to the equipment.
This tool was designed to obtain the maximum possible rigidity, thus allowing an optimum finish level of the machined surface. Furthermore, besides the operation being swiftly carried out, it affords a considerable advantage in that this type of processing gets implemented without the setting of the piece having to be repeated or done on another machine.
The main features of this new patented instrument are:
– A whole operativeness
The same slotting head can be used for both internal and external machinings. It’s necessary to chance the rotation of the motorized axis and turn the head of 180°.
– Simmetry correction
The device placed in the front of the instrument has the purpose to correct simmetry mistakes. As this device leads to a movement of the insert holder along the machine Y axis, thanks to a rail, it is easy to use the motorized slotting head even on lathes with no Y axis. The capacity of the correction device goes from 0,5 mm Y+ to 0,5 mm Y-.
– Longitudinal correction
The ST motorized heads are equipped with a longitudinal correction system which is necessary to guarantee the perfect linearity of the machining. To eliminate possible errors along Z axis, it is necessary to just turn clockwise or counterclockwise the screw placed in the rear part of the instrument.
– Versions
The new motorized slotting head is produced with 3 different slotting depth:
- depth 35 mm: item ST-35
- depth 50 mm: item ST-50
- depth 65 mm: item ST-65
– Tools
The new slotting head will be equipped with special insert holders in all types which have been produced for the machining of keyways and polygonal profiles. The programs for slotting head are available for our customers for free. Each type of motorized slotting head will be used with insert holder with specific machining length: 35 mm, 50 mm and 65 mm.
> UTM series insert holder for machining keyways
> UTM-HEX series insert holder for machining hexagonal profiles
> UTM-SQ series insert holder for machining square profiles
> UTM-S series insert holder for machining special profiles (slots, gearings, evolving gearings, …)
> UTM-M series insert holder for integral inserts
– Machine tool programming
As the experience with programs for standard slotting machining has been a good one, to help using this new instrument, our technicians develped new programs to quickly and easily set up the motorized slotting head. These new programs are suitable for the most popular CNC sfotware now on the market.
– Cutting parameters
To guarantee a lengthy duration of the insert and an optimal machining finish, it is advisable to keep to the suggested parameters (refer to the parameters table).
Maximum thickness obtainable on various materials and cutting parameters: